Surface-Mount Technology (SMT) is a method for constructing electronic circuits in which the components are mounted directly onto the surface of printed circuit boards (PCBs). An electronic device so made is called a surface-mount device (SMD). In the industry it has largely replaced the through-hole technologyconstruction method of fitting components with wire leads into holes in the circuit board. Both technologies can be used on the same board for components not suited to surface mounting such as transformers and heat-sinked power semiconductors.
1. ProtoMat® C20/s
Instant prototypes right out of your lab at a higher level - The ProtoMat® C20/S is setting a new standard in the industry combining the capability to create precision single and double sided PCB's with the operation comfort of a quick-release tool collet and 20,000 rpm motor speed.
|
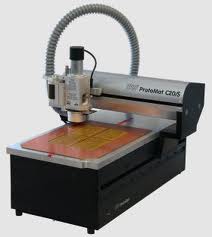 |
2. The LPKF ProtoPrint S
The LPKF ProtoPrint S is a precision manual stencil printer. This tabletop model can be used for prototypes and for small batches of fine pitch SMT boards. Precise vertical separation between stencil and circuit board is guaranteed to meet the specifications of contact printing, as small as 0.3mm (12 mil) pitch (ultra-fine-pitch area).
• On-contact fine-pitch printing
• Parallel stencil separation
• Screen printing
• Printing of populated double-sided boards
• Compatible with various stencil frames
• Test print screen included
|
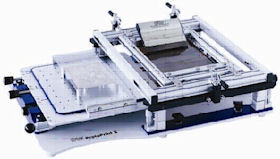 |
3. The LPKF ProtoPlace S
The LPKF ProtoPlace S is an ergonomically designed, semi-automatic pick & place system for the professional assembly of SMD printed circuit board prototypes and small batch projects. The ProtoPlace S quickly assembles SMD boards, with the user controlling each step of the assembly process through an LCD display. Most functions are easily executed from an interface panel with four directional arrows.
• Precise fine-pitch component assembly
• Camera system aids component positioning
• Pneumatic component placement
• Integrated solder paste dispenser
A camera system coupled with the display ensures easy and accurate component positioning control, so the ProtoPlace S can precisely assemble complex circuits.
Manually guided movements of the ProtoPlace S manipulator can be locked in both the X- and Y-directions, and fine adjustments can be performed using micrometer screws. A pneumatic device supports the positioning of the components, eliminating errors and guaranteeing accuracy.
Three different feeders supply the components. An integrated dispenser for solder paste is standard equipment.
|
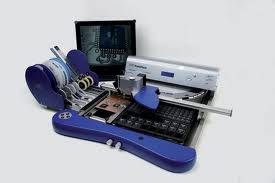 |
4. LPKF ProtoFlow-S
SMD soldering with LPKF ProtoFlow S
The ProtoFlow S is LPKF's premiere convection oven, ideal for lead-free reflow soldering, meeting the stringent demands of rapid PCB soldering applications. The ProtoFlow S features even heat distribution, easy programming, and many pre-defined temperature profiles. The compact design and efficient power consumption make it one of the most useful components in any rapid PCB prototyping environment.
The LPKF ProtoFlow S is a convection oven for lead-free reflow soldering. It is a key component in rapid SMD prototyping and small batch production. Compact and versatile, the ProtoFlow S offers a large working area with motorized drawer for automatic cool-down and easy access, and microprocessor controlled temperature/time profiles. The LPKF ProtoFlow S is excellent for SMD Reflow soldering, adhesive hardening by precipitation, hardening by precipitation of conductive paste for plated-through holes, and other thermal procedures.
The LPKF ProtoFlow S can be fitted with a flow meter for inert gas to prevent oxidation during the reflow process, assuring optimal results of soldered joints.
• Lead-free Reflow Process
• User-friendly LCD display ensures easy operation
• Preprogrammed with industry standard profiles
• Integrated USB communication port for easy programming of reflow profiles and process recording and analysis
• Motorized drawer for easy access and automatic cool-down after reflow process
• Inert gas option prevents oxidation during process
• USB connectivity
|
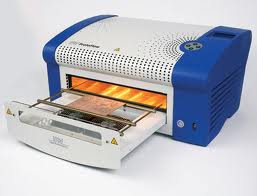 |
5. ERSA REWORK STATIONA
Modular Concept for Maximum Flexibility
• The PL650A is the second generation precision placement system designed for the largest range of components (from 1 x 1 mm to 60 x 60 mm in size), more automation, and greater repeatability. A high-resolution camera with motor zoom permits highly precise alignment of component connections to lands with up to 300x enlargement. The excellent image quality is supported by a high-contrast, separately controlled 2 color LED lighting system from four sides.
• The IR650A Module is a intelligent closed loop rework centre with multiple thermocouple inputs including a non-contact IR sensor offer ultimate control over the selective reflow process.
• The RPC module allows for real time viewing at high magnification of solder-melt and true reflow (Double-drop) and uses a new high-power (up to 300x enlargement) motor zoom camera, a controllable LED ring lighting system, and an extremely robust, movable stand. The reflow process can be visualised from multiple angles on even the smallest of components and due to it s very small eris can view between gaps as small as 5mm to see components leads or ball behind.
• The Auto Pick & Place mode guarantees repeatable and precise (+/- 0.010 mm accuracy) results.
• The IRSoft 3.0 is the Control and Documentation software for the IR/PL 650. This user-friendly software takes into consideration both the interface simplicity required by a less skilled operator, as well as the advanced profiling and documentation wishes of a highly trained user. This professional database incorporated software offers a high level of flexibility and operator customisation capability.
Main Features
• DynamicIR & Multi True Closed Loop temperature control reflow process
• 5 channel temperature recording:
• 1 IntelligentIRS temperature sensor
• ,Laser pointer for component ID
• Motorized reflow head with auto component lift-off
• 9 programmable heating zones with 4,600 Watt
• Integrated axial top & laminar bottom cooling fans
• Integrated RPC camera & movable stand
• Component handling vacuum pen
• Integrated workplace lighting
• Integrated digital soldering station with iron
• System remote control with PC software IRSoft 3.0 via USB interface
|
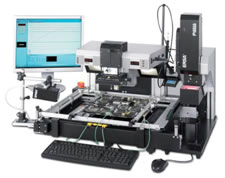 |